copeland scroll digital compressor controller manual
Summary
Find the Copeland Scroll Compressor Controller manual you need. Download it now from Chicago Cashflow and get your system running smoothly.
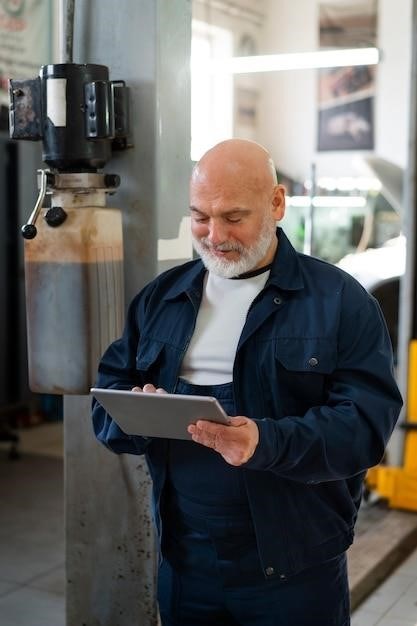
The Copeland Scroll Digital compressor controller is the electronics interface between the Copeland Scroll Digital compressor or the Copeland Discus Digital compressor and the system controller. The Copeland Scroll Digital compressor controller is designed only for single phase Copeland Scroll…
Overview
The Copeland Scroll Digital Compressor Controller serves as the electronic intermediary between Copeland Scroll Digital and Discus Digital compressors and the system controller. This controller is specifically designed for single-phase Copeland Scroll compressors, ensuring seamless communication and control between the compressor and the overall HVAC system. The controller plays a crucial role in managing the compressor’s operation, providing essential protection functions, and facilitating efficient capacity control.
Its primary function is to receive commands from the system controller and translate them into actions for the compressor, ensuring smooth and precise operation. The controller’s advanced features include various protection mechanisms safeguarding the compressor from potential issues like overloads, high discharge temperatures, and low oil pressure. These protective measures enhance the longevity and reliability of the compressor, contributing to the overall stability and efficiency of the HVAC system.
The controller’s capacity control capabilities allow for precise adjustment of the compressor’s output based on the system’s needs, optimizing energy consumption and performance. This adaptability enables the system to respond effectively to changing demands, ensuring consistent comfort and temperature control within the space. Furthermore, the controller facilitates diagnostics and troubleshooting, providing valuable information to technicians for resolving any issues that may arise. This comprehensive approach to compressor management makes the Copeland Scroll Digital Compressor Controller an integral component of modern HVAC systems.
Operation
The Copeland Scroll Digital Compressor Controller operates in a sophisticated manner to regulate the compressor’s performance and optimize system efficiency. It receives signals from the system controller, which typically convey information about temperature, pressure, or humidity levels within the space being conditioned. Based on this input, the controller adjusts the compressor’s capacity, ensuring a balance between cooling or heating output and the actual demands of the environment.
The controller’s core functionality revolves around the concept of pulse width modulation (PWM), a technique that allows for smooth and precise control of the compressor’s operation. By varying the duration of the “on” and “off” cycles of the compressor, the controller effectively modulates the compressor’s output, enabling it to deliver the precise amount of cooling or heating required. This approach offers several advantages, including reduced energy consumption, improved system efficiency, and quieter operation compared to traditional compressor control methods.
The controller’s operation is also characterized by its ability to switch between loaded and unloaded states, effectively adjusting the compressor’s capacity to meet the system’s demands. The loaded state signifies full compressor operation, delivering maximum capacity and mass flow. Conversely, the unloaded state, typically achieved by opening the solenoid valve, reduces the compressor’s output, allowing for a more energy-efficient approach to managing cooling or heating requirements. This intelligent switching mechanism ensures that the compressor operates only when needed, minimizing energy waste and maximizing system performance.
Capacity Control
The Copeland Scroll Digital compressor controller employs a sophisticated capacity control mechanism that allows for precise and efficient regulation of the compressor’s output, adapting to varying system demands and optimizing energy consumption. This control is achieved through a combination of pulse width modulation (PWM) and solenoid valve operation.
The heart of the capacity control system is the PWM signal, which effectively dictates the duration of the compressor’s “on” and “off” cycles. By modulating the pulse width, the controller can finely adjust the compressor’s output, delivering only the necessary cooling or heating capacity. This intelligent approach ensures that the compressor operates at optimal efficiency, minimizing energy waste and maximizing system performance.
The solenoid valve plays a crucial role in the capacity control process. When the valve is open, the compressor operates in an unloaded state, reducing its output and conserving energy. Conversely, when the valve is closed, the compressor operates in a loaded state, delivering full capacity. This dynamic switching between loaded and unloaded states allows the controller to precisely match the compressor’s output to the system’s demands, ensuring efficient and responsive temperature or humidity control.
Troubleshooting
Troubleshooting a Copeland Scroll Digital compressor controller involves a systematic approach to identify and resolve potential issues. This can involve a combination of visual inspection, diagnostic testing, and a thorough understanding of the controller’s operational characteristics.
Begin by carefully inspecting the controller for any visible signs of damage, such as loose connections, broken wires, or burned components. If any visual anomalies are present, address them before proceeding with further troubleshooting. Next, consult the controller’s manual or technical documentation for detailed information on diagnostic procedures, error codes, and recommended troubleshooting steps.
Utilize the controller’s built-in diagnostic capabilities, if available. These features can provide valuable insights into the controller’s status, including error codes, sensor readings, and operational parameters. Analyze this data to pinpoint the source of the problem. If necessary, use a multimeter or other specialized test equipment to measure voltage, current, and resistance at various points within the controller circuit. Compare these readings against the manufacturer’s specifications to identify any deviations.
Error Codes
Copeland Scroll Digital compressor controllers utilize error codes to signal specific faults or malfunctions within the system. Understanding these codes is crucial for effective troubleshooting and repair. The controller may display error codes on its display screen, through a series of flashing LEDs, or through communication protocols with a system controller.
Each error code corresponds to a specific issue, such as a sensor failure, communication error, or overload condition. The controller’s documentation or manual will provide a detailed list of error codes, their corresponding meanings, and recommended troubleshooting steps.
For instance, an error code might indicate a high-pressure switch activation, signifying a potential blockage or restriction in the refrigerant system. Another code might signal a loss of communication with the compressor, suggesting a faulty wiring connection or a malfunctioning compressor module; Consult the manual to understand the specific meaning of each error code and take appropriate action to resolve the underlying problem.
Applications
Copeland Scroll Digital compressor controllers find wide application in various HVAC and refrigeration systems, thanks to their versatility, efficiency, and precise control capabilities. Their use extends across diverse applications, ranging from commercial and industrial refrigeration to air conditioning and dehumidification systems.
In commercial refrigeration, these controllers are commonly employed in supermarkets, convenience stores, and food processing facilities, ensuring optimal temperature control for food storage and preservation. They are also well-suited for industrial refrigeration applications, such as cold storage warehouses, food processing plants, and pharmaceutical facilities.
In air conditioning systems, Copeland Scroll Digital compressor controllers provide precise control over indoor climate, ensuring comfortable and energy-efficient operation. They are particularly beneficial in large buildings, hotels, and commercial spaces where precise temperature regulation is crucial. Additionally, their use in dehumidification systems helps control humidity levels in various environments, such as swimming pools, gyms, and industrial facilities.
Installation
The installation of a Copeland Scroll Digital compressor controller requires careful planning and adherence to specific guidelines to ensure proper operation and safety. The process typically involves several key steps, including⁚
Selecting the Right Location⁚ The controller should be mounted in a location that provides adequate ventilation and protection from moisture, dust, and extreme temperatures. It should also be easily accessible for maintenance and troubleshooting.
Electrical Connections⁚ The controller requires proper electrical connections to the compressor, system controller, and power supply. These connections should be made according to the manufacturer’s specifications and using appropriate wiring and connectors.
Mounting and Securing⁚ The controller should be securely mounted using appropriate hardware to prevent vibration and movement. Ensure that the mounting surface is strong enough to support the weight of the controller.
Testing and Commissioning⁚ After installation, it is crucial to test and commission the controller to ensure it is operating correctly. This involves verifying all connections, calibrating sensors, and checking for any error codes or malfunctions.
Documentation⁚ Keep detailed records of the installation process, including the date, time, and any modifications or adjustments made. This documentation will be valuable for future maintenance and troubleshooting.
Maintenance
Regular maintenance is crucial for ensuring the longevity and optimal performance of a Copeland Scroll Digital compressor controller. A well-maintained controller can minimize downtime, prevent costly repairs, and extend the lifespan of the entire refrigeration system. The following are some essential maintenance practices⁚
Visual Inspection⁚ Regularly inspect the controller for any signs of damage, corrosion, or loose connections. Check the wiring, terminals, and mounting hardware for any signs of wear or deterioration.
Cleaning⁚ Keep the controller clean and free of dust, dirt, and debris. Use a soft brush or compressed air to remove any accumulated particles. Avoid using harsh chemicals or solvents that could damage the controller’s components.
Sensor Calibration⁚ Periodically calibrate the controller’s sensors, such as temperature and pressure sensors, to ensure they are providing accurate readings. Calibration helps maintain precise control over the refrigeration system.
Software Updates⁚ Check for any available software updates for the controller. Updates can address bugs, improve performance, and enhance security. Follow the manufacturer’s instructions for updating the software.
Record Keeping⁚ Maintain detailed records of all maintenance activities, including dates, performed tasks, and any observed issues. This documentation helps track the controller’s history and facilitates future troubleshooting.
Professional Maintenance⁚ Consider scheduling regular professional maintenance inspections and service for the controller. A qualified technician can diagnose potential problems early and perform necessary repairs or adjustments.
Safety
Safety is paramount when working with Copeland Scroll Digital compressor controllers and the associated refrigeration systems. It is essential to follow all safety precautions to prevent accidents, injuries, and damage to equipment. Here are some critical safety guidelines⁚
Electrical Safety⁚ Always disconnect power to the controller before working on it. Ensure that the power supply is properly grounded and that all electrical connections are secure. Use insulated tools and wear appropriate personal protective equipment, such as rubber gloves, to prevent electrical shocks.
Refrigerant Handling⁚ If the controller is part of a refrigeration system, be aware of the refrigerant used. Follow proper handling procedures for the specific refrigerant. Use appropriate personal protective equipment, such as a respirator, to prevent exposure to refrigerant fumes.
Pressure Relief Devices⁚ Never bypass or disable pressure relief devices, such as safety valves or high-pressure cutouts, on the refrigeration system. These devices are crucial for protecting the system from overpressure.
Confined Spaces⁚ If the controller is located in a confined space, ensure proper ventilation and take necessary precautions to prevent oxygen deprivation.
Fire Safety⁚ Always be aware of potential fire hazards associated with electrical equipment and flammable refrigerants. Have fire extinguishers readily available and follow fire safety procedures.
Trained Personnel⁚ Only qualified and trained personnel should work on the controller and the refrigeration system. Ensure all personnel are familiar with the specific safety procedures and equipment.
Emergency Procedures⁚ Develop and communicate clear emergency procedures for handling accidents or emergencies involving the controller or the refrigeration system;
By strictly adhering to these safety guidelines, you can minimize risks and ensure a safe working environment when working with Copeland Scroll Digital compressor controllers.
Technical Specifications
The Copeland Scroll Digital compressor controller boasts a range of technical specifications that ensure its optimal performance and compatibility with various refrigeration systems. Here are some key specifications⁚
Input Voltage⁚ The controller operates on a specific input voltage range, typically between 120V and 240V AC. This voltage range ensures compatibility with standard power sources in different regions.
Output Current⁚ The controller provides a specific output current to power the compressor and other components of the refrigeration system. The output current rating is crucial for ensuring sufficient power delivery.
Communication Protocol⁚ The controller uses a specific communication protocol to interact with the system controller. This protocol ensures seamless data exchange and control over the refrigeration system.
Operating Temperature Range⁚ The controller is designed to operate within a specific temperature range, typically between -20°C and 50°C. This range ensures reliable performance in various environmental conditions;
Protection Features⁚ The controller incorporates various protection features, such as overcurrent protection, overvoltage protection, and short-circuit protection. These features safeguard the controller and the refrigeration system from potential damage.
Dimensions and Weight⁚ The controller has specific dimensions and weight, which are important for installation and space requirements. Ensure that the controller fits the designated installation location and that its weight is within the load capacity of the mounting structure.
Compatibility⁚ The controller is compatible with specific models of Copeland Scroll Digital compressors and Discus Digital compressors. Ensure that the controller is compatible with the compressor installed in the refrigeration system.
Understanding these technical specifications is crucial for proper installation, operation, and maintenance of the Copeland Scroll Digital compressor controller. Always consult the specific controller manual for detailed specifications and compatibility information.