air brake system pdf
Summary
Get your hands on a comprehensive air brake system PDF. Learn about components, operation, and maintenance. Download now!
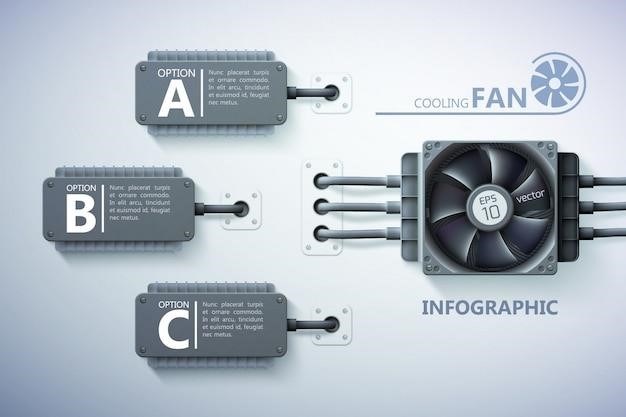
Air Brake System⁚ A Comprehensive Overview
An air brake system is a critical safety feature on heavy-duty vehicles, trains, and other large transportation equipment. It relies on compressed air to activate brakes, providing a powerful and reliable means of stopping. This system is essential for controlling the momentum of heavy loads, ensuring safe operation and preventing accidents. This comprehensive overview will delve into the intricacies of air brake systems, exploring their components, operation, advantages, and maintenance.
Introduction
Air brake systems have revolutionized the transportation industry, providing a safe and efficient way to control the movement of heavy vehicles. This technology, pioneered by George Westinghouse in the late 19th century, has evolved significantly over the years, adapting to the demands of modern transportation. Air brakes offer a distinct advantage over hydraulic brakes, particularly for large and heavy vehicles, as they provide a more robust braking force and are less susceptible to leaks.
The fundamental principle behind air brakes is the conversion of air pressure into mechanical energy. Compressed air, stored in reservoirs, is used to activate brake chambers, which in turn apply force to the brake shoes or pads. This system is characterized by its simplicity, reliability, and versatility, making it a mainstay in commercial trucking, rail transportation, and various other applications. This document will delve into the inner workings of air brake systems, exploring the components, operation, advantages, and maintenance of this essential safety technology.
From basic concepts to advanced technologies, this comprehensive guide will provide a thorough understanding of air brake systems, equipping readers with the knowledge to operate and maintain these critical braking systems effectively.
Components of an Air Brake System
Air brake systems are comprised of several interconnected components that work together to create, store, and apply braking force. These components can be broadly categorized into the air supply subsystem, brake application and release mechanisms, and auxiliary systems. The air supply subsystem is responsible for generating and storing compressed air, while the brake application and release mechanisms control the flow of air to the brake chambers. Auxiliary systems enhance safety and performance, including features like anti-lock braking systems (ABS) and parking brakes.
Key components of an air brake system include⁚
- Air Compressor⁚ This component draws in air from the atmosphere and compresses it to a high pressure, typically around 100-125 psi (pounds per square inch). The compressed air is then stored in reservoirs.
- Air Reservoirs⁚ These tanks store the compressed air produced by the compressor, providing a reserve of air pressure for braking and other functions.
- Brake Valves⁚ Brake valves control the flow of air to the brake chambers, allowing the driver to apply and release the brakes. Common valve types include service brakes, parking brakes, and emergency brakes.
- Brake Chambers⁚ These devices convert air pressure into mechanical force to activate the brake shoes or pads. They are typically located near the wheels and are connected to the brake valves through air lines.
- Foundation Brakes⁚ These are the actual brakes that apply pressure to the wheels to slow the vehicle. They consist of brake shoes or pads, drums or rotors, and mechanisms to adjust the brake force.
Each of these components plays a crucial role in the overall function of the air brake system, ensuring safe and reliable braking performance.
Air Supply Subsystem
The air supply subsystem is the heart of an air brake system, responsible for generating, storing, and delivering compressed air to the braking mechanisms. This subsystem ensures a constant supply of air pressure for brake application and release, enabling safe and efficient vehicle operation. The air supply subsystem consists of several key components, each playing a crucial role in maintaining the necessary air pressure.
The core components of the air supply subsystem include⁚
- Air Compressor⁚ This component draws in ambient air and compresses it to a high pressure, typically around 100-125 psi. The compressor is driven by the vehicle’s engine, using either a belt drive or a direct connection to the crankshaft.
- Governor⁚ The governor regulates the air pressure produced by the compressor, ensuring that it remains within a safe and efficient range. It controls the compressor’s output by cycling it on and off as needed.
- Air Reservoirs⁚ These large tanks store the compressed air produced by the compressor, providing a reserve of air pressure for braking and other functions. Reservoirs are typically made of steel and are designed to withstand high pressure.
- Safety Valves⁚ Safety valves are installed on the air reservoirs to prevent over-pressurization. They release air if the pressure exceeds a predetermined limit, safeguarding the system from potential damage.
- Moisture Eliminators⁚ Air contains moisture, which can freeze in cold temperatures and cause problems with the air brake system. Moisture eliminators remove moisture from the compressed air, preventing it from affecting system performance.
The air supply subsystem is crucial for the operation of air brakes, ensuring a constant supply of compressed air to activate the brakes when needed.
Brake Application and Release
The application and release of brakes in an air brake system is a precise and controlled process, relying on the flow of compressed air through various components. This intricate system ensures smooth and responsive braking, allowing the driver to control the vehicle’s speed and safely bring it to a stop. The process involves a combination of valves, air lines, and brake chambers that work together to create the necessary pressure for brake application.
When the driver applies the brake pedal, the following steps occur⁚
- Brake Valve Activation⁚ The brake valve, located in the driver’s cab, is activated, reducing the air pressure in the brake pipe. This pressure reduction signals the brake system to apply the brakes.
- Air Flow to Brake Chambers⁚ As the brake pipe pressure drops, air flows from the auxiliary reservoirs through the brake valve and into the brake chambers. The brake chambers are located at each wheel, connected to the brake shoes or pads.
- Brake Shoe/Pad Application⁚ The compressed air entering the brake chambers pushes a piston, which in turn applies pressure to the brake shoes or pads, pressing them against the brake drums or rotors. This friction creates the braking force, slowing down the vehicle;
To release the brakes, the driver releases the brake pedal, allowing the brake valve to restore the air pressure in the brake pipe. The air pressure then flows back into the brake chambers, pushing the brake shoes or pads away from the brake drums or rotors, releasing the braking force.
This process of brake application and release is repeated each time the driver uses the brakes, ensuring smooth and controlled stopping.
Types of Air Brake Systems
Air brake systems have evolved over time to meet the diverse needs of various vehicle types and applications. From the simple systems used in early locomotives to the sophisticated designs found in modern heavy-duty trucks and trains, air brake technology has advanced significantly. These systems can be broadly categorized into several types, each with its unique features and applications.
The most common types of air brake systems include⁚
- Conventional Air Brakes⁚ This is the most basic type of air brake system, relying solely on compressed air to apply and release the brakes. It utilizes a simple air supply system, brake chambers, and valves to control the brake pressure.
- Air-Over-Hydraulic (AOH) Brakes⁚ This system combines air pressure with hydraulic components. The air supply system generates compressed air, which then operates a hydraulic pump. The hydraulic pump, in turn, transmits hydraulic pressure to the brake calipers or cylinders, applying the brakes.
- Electro-Pneumatic Brakes⁚ These systems incorporate electronic controls into the air brake system, providing more precise control and enhanced safety features. Electric signals from the vehicle’s control unit modulate the air pressure to the brakes, allowing for features like anti-lock braking systems (ABS) and traction control.
The type of air brake system used in a particular vehicle depends on factors such as the vehicle’s size, weight, and intended use. For example, heavy-duty trucks often use conventional air brakes, while passenger vehicles and some light trucks may use air-over-hydraulic or electro-pneumatic brakes. The choice of system is driven by factors like cost, performance, and the need for specific safety features.
Advantages of Air Brake Systems
Air brake systems have gained widespread adoption in heavy-duty vehicles and trains due to their numerous advantages over other braking systems. These advantages contribute to their reliability, safety, and efficiency, making them the preferred choice for large and heavy transportation applications.
Some key advantages of air brake systems include⁚
- High Braking Force⁚ Air brake systems can generate significantly higher braking force compared to hydraulic brake systems. This is crucial for stopping heavy loads, ensuring that vehicles can come to a safe stop even at high speeds.
- Reliability and Durability⁚ Air brake systems are known for their reliability and durability. They are less susceptible to wear and tear compared to hydraulic systems, and their components can withstand harsh operating conditions.
- Easy Maintenance⁚ Air brake systems are relatively straightforward to maintain. Regular inspections and adjustments, such as checking air pressure, lubricating components, and replacing worn parts, are essential for ensuring optimal performance and safety.
- Tolerance to Leaks⁚ Air brake systems are more tolerant of small leaks than hydraulic systems. This is because the air pressure in the system is relatively high, making it less likely for minor leaks to significantly affect braking performance.
- Versatility and Adaptability⁚ Air brake systems can be adapted to various vehicle types and configurations. They can be used in combination with other braking technologies, such as anti-lock braking systems (ABS) and electronic stability control (ESC), to enhance safety and performance.
The advantages of air brake systems make them an essential safety feature in heavy-duty vehicles, trains, and other transportation equipment. Their reliability, durability, and adaptability contribute to safe and efficient operation, minimizing risks and maximizing safety for both passengers and cargo.
Air Brake System Safety and Maintenance
The safety and reliability of an air brake system are paramount for ensuring safe and efficient vehicle operation. Regular maintenance and inspections are crucial for identifying potential issues and preventing accidents. Proper maintenance practices contribute to the longevity and performance of the system, minimizing risks and maximizing safety.
Here are some key aspects of air brake system safety and maintenance⁚
- Pre-Trip Inspections⁚ Before every trip, a thorough pre-trip inspection of the air brake system is essential. Drivers should check the air pressure gauges, inspect for leaks, and ensure that all components are functioning correctly. This includes verifying the brake pedal feel and ensuring that the parking brake is engaged and released properly.
- Regular Maintenance⁚ Regular maintenance includes checking and adjusting brake shoe wear, replacing worn brake components, and lubricating moving parts. Inspecting and cleaning air lines and filters to prevent blockages and ensure proper air flow is also crucial.
- Air Compressor Maintenance⁚ The air compressor is a critical component of the air brake system. Regular maintenance involves checking the compressor’s oil level, inspecting the intake filter, and ensuring that the governor is functioning correctly to maintain proper air pressure.
- Emergency Brake System⁚ The emergency brake system is a backup safety feature that should be tested regularly. This ensures that the system can be activated in case of a failure in the service brake system. The emergency brake system should be able to bring the vehicle to a safe stop.
- ABS System⁚ Vehicles equipped with Anti-lock Braking Systems (ABS) require regular maintenance to ensure their functionality. This includes checking the ABS sensors, the modulator valve, and the control unit to ensure that the system is operating correctly.
By adhering to these safety and maintenance practices, drivers and technicians can ensure the optimal performance and reliability of the air brake system. This reduces the risk of accidents and promotes safe and efficient vehicle operation.
Troubleshooting and Repair
Troubleshooting and repairing an air brake system require a methodical approach and a thorough understanding of its components and operation. It’s essential to identify the problem accurately before attempting any repairs. This involves a combination of careful observation, diagnostic testing, and knowledge of the system’s workings.
Here are some common troubleshooting steps and repair considerations for air brake systems⁚
- Identify the Symptom⁚ The first step is to identify the specific symptom or problem. Is the vehicle experiencing a loss of braking power, a slow build-up of air pressure, a brake pedal that feels spongy, or a warning light indicating a system malfunction?
- Inspect for Leaks⁚ Leaks in the air brake system are a common cause of problems. Inspect all air lines, connections, valves, and brake chambers for leaks using a soapy water solution. A leak will create bubbles in the soapy water.
- Check Air Pressure⁚ Use the air pressure gauges to check the system’s pressure. The pressure should be within the manufacturer’s specifications. Low air pressure can indicate a leak, a malfunctioning air compressor, or a problem with the governor.
- Test Components⁚ Test individual components of the air brake system, such as valves, relays, and switches, to ensure they are functioning correctly. Use a multimeter to check for continuity and voltage in electrical components.
- Inspect Brake Chambers⁚ Inspect the brake chambers for damage or leaks. Check the brake shoes or pads for wear and replace them as needed. Inspect the brake cylinders for leaks or damage. Ensure that the brake shoe adjustment is correct.
Remember that repairing an air brake system requires specialized knowledge and tools. If you are not comfortable working on the system, it’s essential to consult a qualified mechanic.